No. Don't. Don't tell me this, don't do it to me, I'm trying to complete Satisfactory playthrough
Oh my God, these new subclasses are going to get me back into the game. The sorcerer and cleric subclasses.. ah!
I mean, yeah. Obviously. But to the other businesses or potential business owners that want to try a tipless model, that see these businesses failing, that's not very encouraging or helping to figure out what the underlying issue is. If people are trying to do a good thing but can't quite figure out how to make it work, should we just say, "guess you're not very good at this" and continue giving business to the places asking for tips, or should we try to look into what's going on?
I generally agree with you, but what is your response to businesses like those mentioned in the article that tried a no-tip model and could not sustain it?
I think that tipping models are starting to emulate app microtransaction models - they know that a majority of people are not going to tip, or will round their total up to the nearest dollar or something. It's the person that sees the option to tip and decides to throw an extra $20 just because that they're after. If they instead raise the prices to make it average out, the majority of people that normally would not be tipping go somewhere that's cheaper (because they do tips), and the few people that would pay extra no longer have the option to.
To tie back to the microtransaction analogy - the games that bring in money are the free ones where you can pay to get stuff. Most people pay very little or nothing, but a small percentage throws tons of cash into the game. If you were to take the amount of money brought in by these whales over the life of a game, divide it among all people that played it, and charged that much for the game, it wouldn't profit nearly as much, because none of those people want to pay the $5, and the people that were spending hundreds can only buy the game once, if that.
I think a big flaw in your thinking is that you aren't considering that we still have all the people currently living to take into consideration. We wouldn't be instantly reduced to a tiny population that is easy to restructure and organize, there's still like 8b people on the planet, and none of the ones in charge are going to just say, "oh, well I guess none of this matters anymore, let's focus on sustainability".
It would take a couple years for us to see a significant decrease in population, and all the while, those currently in power would remain in power. We wouldn't suddenly drop to a few thousand like minded individuals, all ready to work together to rebuild. We'd be a declining population that is scared and clueless how to save itself, making mistake after mistake.
"That thing you like, is actually not good and you don't like it. Get something better" why are coffee people like this 😭
Re: wrenches.
I'm not sure where you're at or what kind of things you will be working on, but here in the US you generally want to have at least a cheap set of both SAE and Metric wrenches. Nothing is more frustrating than having a random bolt be SAE while everything else is metric, and stripping the bolt with a wrench that is "close enough".
You'll also come to a decision on if your like flat wrenches or angled ones, though it doesn't hurt to have a cheap set of both.
If you know for sure what set you'll be using the most (or even better, what sizes you'll be using the most), spending a little extra money on "ratcheting" wrenches can save you a ton of time and frustration. I do a lot of toying around on my car, and some of these bolts are in tight places where you can't turn a wrench very far; ratcheting wrenches let you get the wrench in place once and just wiggle the bolt out.
One time the homie showed me a meme of some stock performance charts and I just could not stop laughing
If the company wasn't constantly buying stupid shit like this and spending money on the most inefficient systems ever, I'd be more inclined to agree with you.
Idiotic business decisions are the recurring costs.
Example: We have a new program in place that is supposed to "balance" inventory across locations. My pharmacy has sent and received the same specialty medication back and forth to another location on the other side of the country 3 times now, with neither location having actual need for the medication. I'm sure we've got a good corporate deal with FedEx, but there's expenses outside of shipping costs (namely pharmacy labor hours) that we're expending to literally just ship a box back and forth across the country. And if we don't do it, they'll come harassing us to see what the "issue" is.
Yeah wtf is the first part supposed to have to do with the last line or image
It's not just in education.
Retail pharmacy. My company ~2 years ago decided to start offering clinical services to patients - great! In my store, they walled off part of what used to be the stockroom, expanding our waiting area and giving us a dedicated vaccination room (previously in a sectioned off part of the waiting room) and a health care room (where all the new services went).
To support these new services we got all kinds of really fancy tech - 20 inch 1440p (?) touchscreens for check-in. Very high end blood pressure machines. Two (2) computers in the healthcare room for the one (1) healthcare provider, because, you never know. These changes can be seen in a majority of this company's stores.
If you haven't guessed by now, they've decided to not go through with those clinical services. All of the tech we bought (if I had to estimate, very conservatively, $15k USD for my store) is either reboxed or installed but powered off on the sales floor, has been for ~12-18 months, and has no plans of ever being repurposed or sold. The vaccination room serves zero additional purpose to the area we had before, and the "healthcare room" is now used as the pharmacy stockroom (since, y'know, they removed part of the stockroom to build it). This is all ignoring the money spent on actually building these rooms (with lighting and climate control nicer than the rest of the store) and profits lost during construction.
But we don't have enough money for raises, or enough hours to functionally staff the pharmacy 🙃
Yeah I don't even get what is supposed to be the taboo thing that is sending the person to hell on this one. It's literally just a benign pun
Oh no, he's snuck his way in with you guys now? Christ, we're really pulling Canada down with us, aren't we.
Big "I don't need you to make me look stupid" vibes right here
Nobody:
The paywall my country has set up (my 70th birthday is behind it):
I see. It came out clean.
If I may make a suggestion for if you make a similar design in the future, there is a model I found for a dice tower that has a logo indented maybe 0.2mm on the front of case. You print this side face down on the plate, it prints the face with the logo cut out; swap the filament before the following layer, and it will print mostly smooth against the build plate with your contrasting color.
Of course, what you've done comes out with a thicker indented logo, so if that's what you're looking for this wouldn't be the same look, but just wanted to throw the idea out there in case you wanted to play around with it for the future.
Well done! Big fan of the two tone finish.
Was the top piece printed as a single part with a filament swap part way through, or is it two separate pieces stuck together?
What if I'm the person I'm upset with 🤔
Life...
You could say it started when I was a kid.
Like most people, I was different. But not like the others.
Holy shit, he is so wise
Thanks for providing these, I'll take a look when I've got a minute.
An elf.. druid.. mermaid... Thing.


This is one of the characters from Valandar's second Player Character pack. His weapon made me think of mer-people, so I wanted to paint this guy with an aquatic theme. About halfway through I realized the color scheme wasn't going in the direction I wanted, so I abandoned the aquatic theme and just picked colors that I thought would look good together.
After applying the final wash, I felt the model looked too dark and monotone, so I decided now was a good time to give edge highlighting a try, something I've always been too lazy or impatient to try. Holy crap, does a tiny bit of white make a difference! You can see that my blending and edge selection leaves plenty to be desired, but for a first time, I think some parts of his robe look really cool.
As always, here are a few more angles:
If anyone has any advice or pointers for color selection, I'm all ears. For this guy, I started with the color I knew I wanted to make a bulk of the model (blue/ aquamarine), picked a few nearby colors (green and purple) for the secondary bits, then jumped across the color wheel (yellow and gold) for the highlights. I think the model has good contrast, and the colors look ok together, it just doesn't have the look I was going for. I'm sure I'll get a better eye for color selection as I continue to paint, but if there are any places to start looking I'm open to pointers.
Brrr! Icy orcs coming your way!


I realized that I never posted my complete army of Ice Orcs that I'd posted a WIP a little bit ago.
Here they are! Some of them definitely turned out better than others, but I had a lot of fun painting them up and I'm happy with how they look as a whole. I've only ever painted one other "army" of minis, and I used the same color scheme for all of them, thinking I needed to in order to make them look like a cohesive unit. It worked, but just as they were cohesive, they were boring.
I tried a different approach here, picking out a general list of colors (black, brown, tan, and gray) that fit the theme I was going for. For each orc's armor, I mainly stuck to the selected colors, but threw them on wherever I thought it would look good, not caring if the previous model was brown with black accents, black with tan accents, etc. I figured as long as they all used them same colors overall, the colors would tie themselves together.
The skin came out a little wonky, but if you've seen my other posts or comments, you'll know that was kind of expected. I'm pretty ass at painting skin tones, and used the orcs as a playground to hone the skill a bit. They still don't look great, but I'm getting better at things like highlighting muscles and shading skin folds and the like.
Anyways, sorry for the giant wall of text. Here's a few glamor shots, featuring my paladin from a few weeks ago.
A generic adventurer. Please, do not look at his face.


You looked, didn't you.
This is slightly different than my normal paint jobs. As evidenced by the background of the picture, he was painted using only cheap craft paints (save for the sword and other metallic highlights). The reason for this is that I plan on hosting a Mini Painting Party, where I'll be providing all the supplies needed to paint up some little dudes. I want to do this without breaking the bank, but I also wanted to make sure that the cheap paints weren't going to make the experience unenjoyable. So, I put together the same kit I plan on giving everyone (#0, #1, #2 brushes, a DIY wet palette and some toothpicks) and got to work.
I've got about a dozen of this same mini. I might tweak the color scheme a bit, but the plan is to teach everyone step-by-step how to replicate the above, then bust out the assorted minis once everyone has an idea of what they're doing. Originally, I was going to pull the nice paint out after the first mini, but after seeing how well the cheap stuff held up, I think I'll save the pricey stuff for myself...
That being said, the craft paint worked much better than I was expecting. Part of it is likely due to the experience I've gained since I last used the stuff, but the only time I felt frustrated with the paint was when applying the final wash a good amount of green washed off. This happens to me a lot when applying washes so I think it's more something I'm doing than the paints fault, but it was much worse with this craft paint than the nicer stuff.
Anyways, here's a couple other angles.
Orc Horde, ice skin variant


This is a work in progress pic of what will eventually be an army of icy blue-gray skinned orcs. I plan on making a range of colors between pure light gray and pure baby blue, and grabbing colors from different parts for each orc so they'll all have different but similar skin tones.
The models are from Valandar's awesome Orc Horde collection on Thingiverse. These models are a ton of fun and a great balance between high-detail and printability/ paintability. I wish the bases were a little more interesting, or printed separately so I could attach my own, but a flat base allows me to add my own terrain later on.
I plan on doing a typical green-skinned orc army, as well as a fire-red army. Orcs are a fun way to play around with different armor color schemes because if something ends up looking like crap you can just say, "they're orcs! They just grabbed what's available!"
A blue-skinned, half-giant barbarian.


This is my friend's character for a campaign that we are in. He used AI to create the general look of his character, then designed a mini based on the outcome. I printed it out for him and used the AI image as a color reference.
Here are a few other angles:
And here is the AI generated image that the mini is based off of:
(The small girl is the character's sister.)
A (slightly larger than mini) mindflayer


This is my paint job on Yasashii's "Mind Flayer / Illithid Tabletop Miniature" from Thingiverse.
This was one of the first prints off of my resin printer, and the first piece I attempted air brushing; to make both of these a little easier, I scaled him up a bit, so he isn't quite "tabletop minature" scale, but still much smaller than what I'd been used to painting (~70mm tall).
Everything except for the red eyes and purple highlights on the armor was done with a 0.3mm airbrush.
Here are a couple different angles:
Unfortunately one of the robe dangly bits snapped off the back before I could start painting. I didn't expect the paint job to turn out this decent so I didn't bother reprinting, kinda wish I had.
A generic paladin adventurer


This is a miniature from TitanCraft's "RPG Mini Starter Kit" on thingiverse. I painted him up just to get some practice painting minis as I'm just starting out on the small scale stuff.
Here he is from a couple of different angles:
I wish that the paint on his face came out a little better, it's something I've always struggled with.
I may be preaching to the choir here, but if you haven't already heard of it, check out TitanCraft. It's another mini maker website, but you can actually download minis that you make for free (they have paid and free assets, but there's a ton of free ones and you don't have to pay anything to download an all-free model). I'm not affiliated with them in any way, but I've been showing it to all my DnD friends and a few of them are sending me minis to print out for them, and it costs us nothing but the $0.25 of resin.
Why are default lift distances so high?
I've been resin printing for maybe a month. I've noticed that on all of the resins that I've got, and all of the profiles I've downloaded for them, the lift speed is usually at least 3 to 4 mm. However, when listening to my printer operate, I can tell that it is fully separating the print within the first millimeter or so. I've changed almost all of my resin profiles to only lift 1 mm, cutting each layer time down like 2 seconds, and absolutely zero change in any quality whatsoever. Am I just lucky with my printer configuration, or my fep is especially tight? Or why else would such a large distance be commonly recommended?
Is there a way to view posts that I've "hidden" with the little checkmark?
I'm dumb and sometimes tell my phone to do things I don't actually want it to do, like hide posts I actually want to check out. I can't find a way to look at those to bring them back.
Message icon doesn't go away from private messages
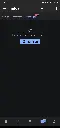
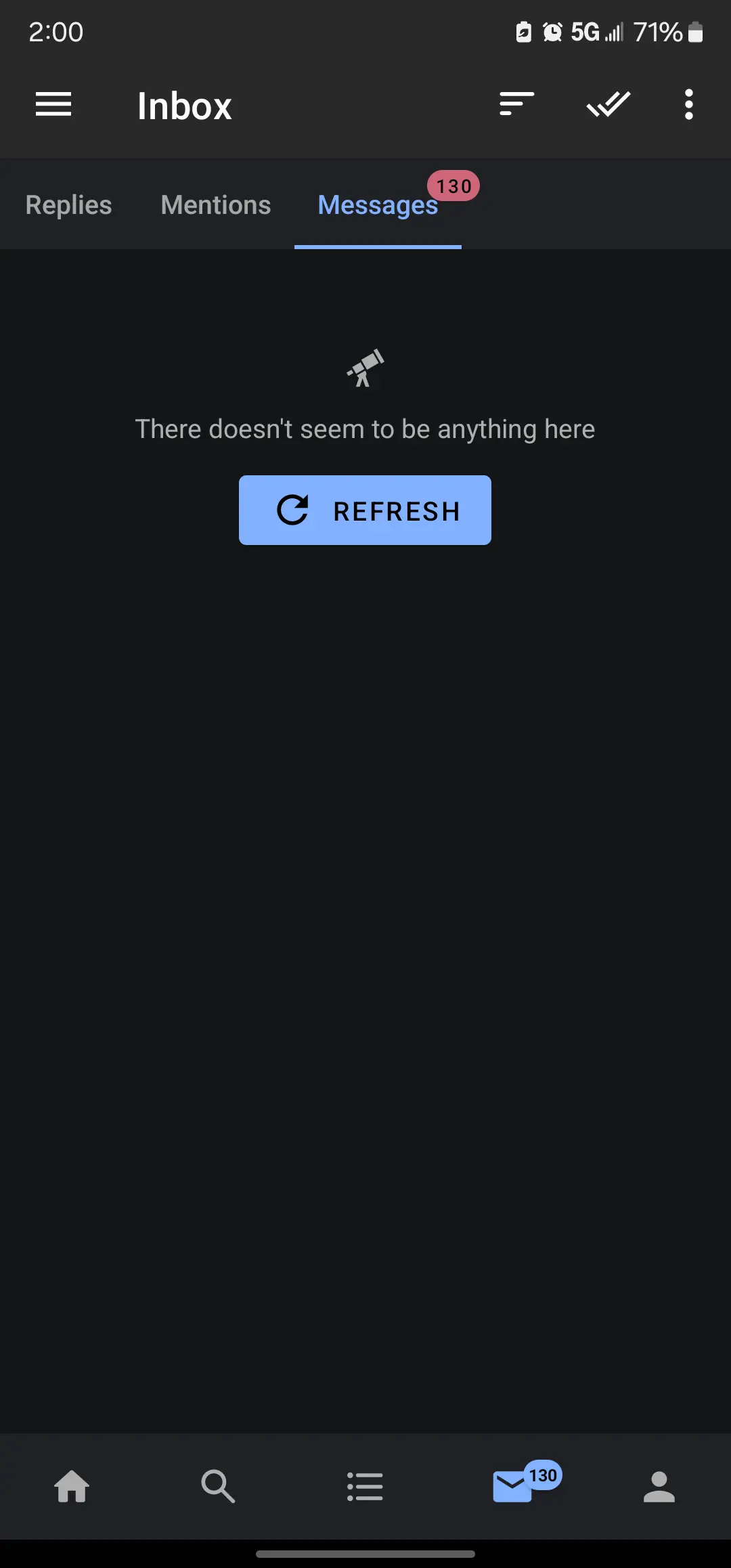
I've been helping someone diagnose a technical issue through Lemmy PM's the last month or so, and have accumulated a lot of messages back and forth. (Around 130 I'd say.)
When I get a new message, the total number of messages that I've received shows as a notification for a while, until it eventually disappears. (I haven't fully tested it but I think it disappears on reboot once I've replied.) Receiving comment replies or a new pm brings the notification back.
The screenshot shows what I see when filtering for unread messages. Thus, there are no unread messages, let alone 130 of them.
The entire conversation has been had in the same message thread. Not sure if this is a Lemmy issue or boost issue.
How can I read the layer height from a gcode file and pass it on as a variable?
Hi all, got a bit of a technical problem I'm trying to solve and I've got very little programming experience.
Basically, I'm trying to create a folder with a bunch of filament profile cfg files, with things like retraction distance, temperature, flow rate etc preloaded into them. That way, I can slice a model for a 0.6mm nozzle, send it to Klipper, and run it with any filament I want without having to re-slice, just change which cfg file is loaded.
This is going pretty well and I've figured out how to get most of what I want into the cfg. However, I want to limit my print speed by my maximum volumetric flow rate, a variable that Klipper does not support (and Kevin has more or less denied requests to have it added). To solve this issue, I want to limit the max speed instead, using a formula like this:
print speed = (max vol. flow) / (nozzle width) / (layer height)
(max vol. flow) and (nozzle width) would be defined manually by me for each profile. The only issue is (layer height), which of course can change from print to print. I know that my slicer puts the layer height and total number of layers in the header of the gcode, I also understand that that's where Klipper gets this info from and how it displays those numbers once you've selected a file. What I'm having trouble figuring out is how I can send that number into the above formula; I found this which seems to be almost what I need, but I can't figure out how to use the "print_stats object" in my cfg.
A potential workaround is to find my maximum layer height for each nozzle/filament combo and set the max speed assuming that later height, but if I'm printing something at say half my maximum layer height that's going to severely unnecessarily reduce my print speed.
Any advice?
"View the rest of the comments" only showing one additional contextual comment
When viewing a single child comment thread (ie viewing a response to your comment that is already a few comments deep in a thread), you are given two options at the top of the comment section, one to "view full context" of the thread you're in (expected behavior: give context up to the parent comment and show only comments in that thread) and one to "view full comment section".
As of now, at least for me, both options simply give me one additional parent comment above what I can already see (in my previous example, it would show the comment I originally replied to). To get to the full comment section, I have to press the option and reload the comment section over and over until I get to the parent comment, at which point "view full comment section" actually does what it says.
Random EOF shutdowns from Klipper.
Hi everyone, a week ago my printer (heavily modified Neptune 3) started randomly shutting down in the middle of prints. I come back to a print with the "Klipper reports: SHUTDOWN / Lost communication with MCU 'mcu'" error message.
The printer has been "under construction" for the last couple of weeks, but it has been in varying states of "working" for most of the time - working well enough for me to print the parts I needed to get it back to "fully operational". During this time, the printer never shut down like it is now.
Only once I started making little cosmetic changes did the problem present itself. I was running a known-good print, and I got the above error twice (first time after ~2 hours, second time after ~1 hour) before I got a successful print off of it. This was last week.
After this successful print, I continued other prints with no issues. After a day or two with no problems, an hour long print threw the error at me four consecutive times between 10-45 minutes into the print. This is when I started looking into my klippy log and found some relevant articles citing things like EMF interference, bad power supplies, faulty cables etc. I realized that one of the changes I had made rerouted the printer USB cable right around the Z-stepper, so I rerouted it to how it was originally and immediately managed a successful print. This was 5 days ago.
After moving that cable I had no issues with printing several-hour long prints... until last night. I had been printing all day, then the problem came back. After one print finished, I queued up another print with a plate full of parts, it failed after 1.5 hours. Tried the same print again, failed in 30 minutes. I re-sliced to only a handful of parts to see if I could get those to print before the error occurs, and it's failing 15 minutes into the print.
The printer power supply is the unit that came with the Neptune, and it isn't powering anything besides stock hardware (exception being the SKR mini board), so I don't think it's that. The pi is on a quality unit. The USB cable has been working for a long time so I also don't suspect that, but I'm probably going to buy a new one today just to be sure. I adjusted my enclosure setup so that the Pi and SKR are able to get cool air (at one point had a personal fan pointing at the open electronics box, still failed).
Here is a link to my most recent klippy log (abridged to the start of the last failed print). I'm not very familiar with reading through this and finding oddities, but I do think it's strange that it seemed to load my preheat script in the middle of printing right before the EOF error. (It should be noted that this preheat script was made 1 or 2 failed prints before this most recent one, so it isn't the source of the error as prints were failing before the script was made). If there's anything I'm missing or something else I can try, please let me know!
Edit: While typing this post, I was running the same failed print without filament and both heaters turned off. It ran for about 45 minutes (most recent failure occurred at 12 minutes) so I cancelled the print and started it again with heaters turned on, still without filament. It again ran for about 45 minutes, so I again cancelled it and started the print again, this time with filament loaded. It failed in 5 minutes.
Edit 2: A test print with heaters on and no filament failed after 1h8m. So it isn't an issue with extruding filament.
Edit 3: New cable with the 5v leads taped off per @SzethFriendOfNimi@lemmy.world's advice. Ran the print without filament until completion. Reloaded the same file with filament, print ran without issue until the 1h14m mark, at which point I tapped my Klipperscreen device to wake up the screen, and as soon as it displayed the status, the printer errored out. This can't be a coincidence, can it? Whenever the print goes unmonitored for a long time, it fails as soon as I do something (load mainsail, turn on the klipperscreen) to check the status of it.
Any thoughts on a fully printed voron?
Hi guys, been thinking about this for a couple weeks now but can't seem to find anything online about anyone who has tried it.
I'm considering converting my printer into a voron. However, since I currently have a fully functioning printer, I wondered why I can't print the extrusions rather than purchasing them? Of course they are larger than my printer's volume, but there was this video posted here a while back about a great way to create strong permanent joints for parts just like this:
https://youtu.be/zI8OgRRF5d8
The way I would do this would be to model the extrusions as a solid piece and make cutouts in the areas that bolts are meant to be ran through.
Is this even within the realm of possibility, or is there a specific barrier that has prevented others from trying this? The obvious concern is stability/ rigidity, but if everything is printed at voron part standards or thicker with an infill pattern like gyroid, would the decrease in rigidity be too much for input shaping to compensate for?
Thanks for any ideas or input! If there aren't any major road blocks or examples of this failing I think I'll try it out once I've got the space for it.
My makeshift enclosure filament holder. Very happy with this set-up!


Hi guys, it's The Clog Guy, thought I'd try to share something other than problems...
Shortly before my printer went kaput again, I designed and printed a bracket to move my Bowden extruder to the hotend, making my printer a direct drive variant.
This posed an issue: I now needed to feed filament from the top of the printer rather than the side, where I previously mounted my filament holder.
I also have the issue many of you probably do where I am running out of room for my many filament spools.
Enter: The Rod. Two holes on either side of the enclosure, and I can hold probably 8 or so spools within the enclosure.
The Rod slides out on one end to allow for quick spool changes:
And I even had the foresight to put a clamp on one end to prevent it from getting yanked out all the way:
I canabalized the filament guide from the printer to the top of the enclosure with one screw so it would swivel, put those thumb tacks in to keep it from spinning all the way around, and the enclosure is ready to go!
Now if only my printer worked...
Clog Guy is back, and things have completely ceased making sense.
Hi guys. Please check my previous post for any background questions, I don't have it in me to go over everything again.
Long story short, I was having issues with clogging that were being caused by my hotend not reaching the reported temp. After a few days of troubleshooting and diagnosing the motherboard and Klipper settings, I gave up and decided the motherboard was faulty (even though I could not perform any tests to determine in) and bought an SKR mini. I got that all set up, and the printer has been working flawlessly since then.
Until now.
Same exact problem; one print goes perfectly fine, next print, failing to extrude by the 4th layer. I removed the clog, restarted the print, now can't even extrude the priming line. Fearing the worst, I disassemble the hotend, try hand feeding filament, and once again I am unable to push more than a few centimeters through before it gets clogged up. A probe thermometer reads ~160C while Klipper reports 200C.
What could possibly be happening here? The board is an aftermarket replacement from a completely different company, so I doubt it's a recurring manufacturer defect, but I have no idea what else can be causing this.
At this point I've spent so much time and money trying to fix this printer that I could almost buy a new one, but at this point I'm not convinced even that would solve the problem.
"Show x more replies" while viewing a comment with parent comments hidden displays additional replies with full context markers (see photo)
I couldn't find a great way to describe what I'm seeing. But if you're deep in a comment thread, or viewing a reply to your comment, and have parent comments collapsed, if there are additional comments, choosing to show them adds the number of context indicators (the little lines on the left) that it would have were the parents not hidden.
!Bug
The comment from FlyingSquid was the comment hidden by "show 1 more reply".
It's the clog guy again - temp readings are bad!
OK guys, I finally found what the issue is, or at least kind of where it's coming from.
As some of you (and myself) suspected, my hot end is not reaching the reported temperature. I previously blamed the low readings on my IR thermometer on not being able to point the laser directly at the hotend, but it seems it was reporting accurate readings (around 95C when klipper reports 200C).
Now, here's where things get a little weird. At this point, I've used multiple thermistors, but swapped in a new one anyways. My board also has a pin for a second extruder thermistor, so I plugged it in to that one and changed the pin in my printer.cfg. No change.
I tried switching the bed and hot end thermistors on the board and in printer.cfg, no change.
I changed the thermistor "sensor type" from "EPCOS 100K B57560G104F" (same as the bed) to "Generic 3950", no change.
I found an article about tuning your pullup_resistance value. My cfg file did not have this value specified, so I added a line and started with the default of 4700, which made no difference (I'm assuming this value is loaded from the sensor type by default?). I toyed with the values until my thermometer read ~220C when setting the printer to that temp. However, to achieve this I had to adjust the pullup_resistance from 4700 to 13k+ (far beyond what should be needed) which makes klipper report 6C at room temp (print bed reports 27C). Unsurprisingly, I can hand-feed all the filament I want, but the temp reading is only now only accurate at 220C rather than only being accurate at room temp.
The thermistor, I feel, can be removed from the suspect list, as multiple thermistors exhibit identical properties.
I also feel the motherboard can be removed as well; there are three pins for thermistors, all three show accurate readings for the bed but identically inaccurate readings for the nozzle.
This only leaves software/ firmware, which I find incredibly odd for three reasons. For one, the printer was not even shut off in between "working" and "not working"; I successfully completed a print, and without shutting down, updating any configs, changing any settings etc., I swapped out the nozzle, and the printer hasn't worked since. Second, both the bed and nozzle thermistor are configured exactly the same, so if the nozzle is not set up properly the bed should be wrong too. Finally, Klipper is really straightforward and it's easy to configure things that commonly need configuring, it doesn't seem right that a configuration got changed and I'm completely incapable of finding what happened and fixing it.
As a Temporary FixTM, I'm inclined to get a nice reliable probe thermometer, calibrate a pullup resistance value for common print temps, then updating my cfg whenever I want to change temps more than ~5c. This is obviously not even close to an ideal solution, but I don't know what else to try. Everyone else I've seen with this issue has resolved it either through hardware replacement or fixing settings, and I've tried all I can with both.